With the advancement of industrial automation and precision manufacturing, CNC (Computer Numerical Control) machine tools have become an essential part of modern production. These machines rely on high-performance control systems to achieve precise cutting, milling, and engraving. One of the key components ensuring the efficiency and precision of CNC machine tools is the Variable Frequency Drive (VFD). This article explores the role of VFDs in CNC machining, particularly in spindle control, and how they contribute to improved performance and efficiency.
The Structure of CNC Machine Tools and the Role of VFDs
CNC machine tools consist of three main systems:
- Host Machine:This includes the machine bed, spindle, feed mechanisms, and supporting mechanical components responsible for executing machining operations.
- CNC Control System:The core control unit consists of hardware and software responsible for processing digital input, executing interpolation calculations, and controlling motor movements.
- Drive System:This system comprises the spindle drive unit, feed drive unit, spindle motor, and feed motors, all of which work under the control of the CNC system to execute precise movements.
Among these, the spindle system plays a crucial role in determining machining accuracy and efficiency. The VFD is a critical component in spindle drive systems, ensuring smooth speed control, energy efficiency, and improved machining quality.
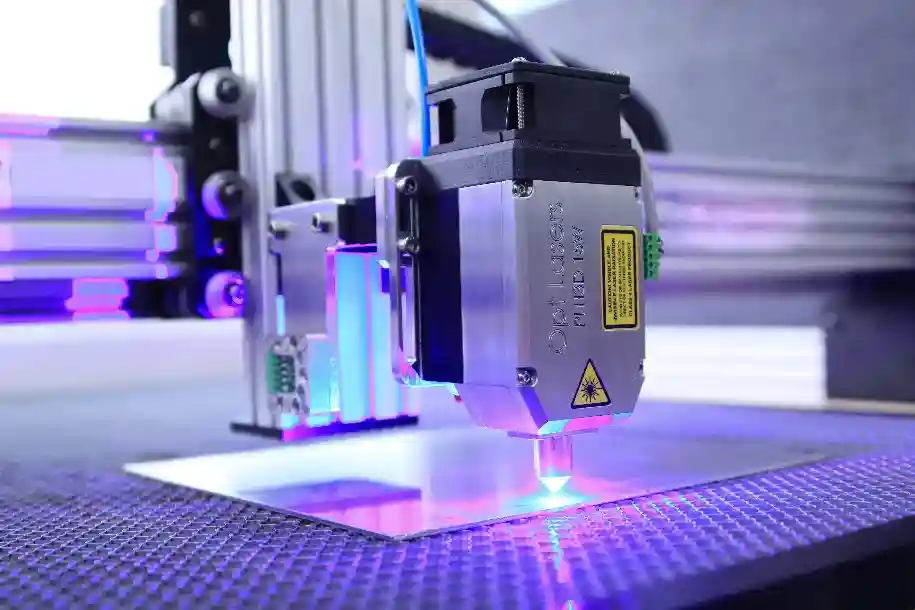
Why VFDs Are Essential in CNC Machine Tools?
CNC machining requires precise speed control of the spindle motor to accommodate different cutting conditions. The traditional fixed-speed spindle motors lack flexibility, leading to inefficiencies and limitations in machining processes. This is where VFDs provide significant advantages:
1. Precise Spindle Speed Control
- VFDs adjust the spindle motor speed seamlessly by regulating the frequency of the power supply.
- They allow for a wide speed range, enabling different cutting speeds for various materials and machining processes.
- Through digital control, CNC systems can directly program the spindle speed for optimal performance.
2. Soft Start and Acceleration Control
- Conventional direct-on-line (DOL) motor starting methods generate high inrush currents, leading to mechanical stress and potential damage.
- A VFD provides a smooth acceleration curve, reducing mechanical wear and extending the lifespan of spindle components.
- The ability to control ramp-up and ramp-down times improves safety and reliability.
3. Enhanced Machining Quality
- By ensuring stable and consistent spindle speed, VFDs minimize speed fluctuations, which could otherwise cause irregular cutting patterns or tool marks.
- Dynamic torque control enhances cutting precision, particularly in high-speed engraving and milling applications.
4. Energy Efficiency and Cost Reduction
- VFDs optimize energy consumption by adjusting motor speed to match actual machining requirements.
- Unlike traditional systems where motors run at full speed regardless of load, VFDs reduce unnecessary power usage, leading to significant energy savings.
5. Integration with CNC Systems
- Modern CNC machines require real-time control of spindle speed.
- VFDs can communicate with CNC controllers via industrial communication protocols (such as Modbus, Profibus, or EtherCAT), allowing for seamless integration into automated machining workflows.
Application of VFDs in CNC Engraving Machines
CNC engraving machines are widely used in industries such as woodworking, metal processing, advertising, and mold manufacturing. These machines rely on high-speed spindle rotation to achieve precise cutting and engraving. The VFD plays a central role in controlling spindle speed and optimizing performance.
How VFDs Work in CNC Engraving Machines:
Software Design and Signal Processing:
- The user designs patterns or tool paths using dedicated engraving software on a computer.
- The control system converts this data into electrical signals for motion control.
Motor Control and Spindle Operation:
- The CNC controller sends signals to the VFD, instructing it to control the spindle motor’s speed and torque.
- The VFD adjusts motor speed dynamically based on material type and cutting depth, ensuring optimal performance.
Real-time Adjustments for Different Materials:
- Soft materials (e.g., wood, acrylic) require high spindle speeds.
- Hard materials (e.g., metals, stone) require lower speeds with higher torque output, which VFDs efficiently manage.
By using a VFD-driven spindle system, CNC engraving machines achieve superior surface quality, reduced tool wear, and improved operational efficiency.
VFD Selection for CNC Machine Tools
When selecting a VFD for CNC applications, consider the following factors:
Power Rating and Voltage Compatibility:
- Ensure the VFD matches the spindle motor’s power rating and operating voltage.
Speed Range and Control Precision:
- A good VFD should provide a wide frequency range (typically 0-400Hz) for optimal speed flexibility.
- High-resolution speed control is essential for precision machining.
Torque Performance:
- Look for vector control or sensorless vector control (SVC) for better torque regulation at low speeds.
Communication and Integration:
- The VFD should support communication interfaces like Modbus, CANopen, or EtherCAT to ensure smooth integration with CNC controllers.
Protection Features:
- Overvoltage, undervoltage, and overload protection ensure reliability and prevent motor damage.
Conclusion: VFDs as the Backbone of CNC Precision
Variable Frequency Drives are revolutionizing CNC machine tools by enhancing spindle control, improving energy efficiency, and increasing machining accuracy. Their ability to dynamically adjust speed and torque makes them an indispensable component in modern CNC systems.
As industries demand higher precision and efficiency, GTAKE’s advanced VFD solutions provide the reliability and performance needed for CNC applications. Whether in high-speed engraving or heavy-duty milling, GTAKE VFDs deliver superior control, energy savings, and long-term operational benefits.
If you’re looking for high-performance VFDs for CNC machine tools, contact GTAKE today to discover how our solutions can optimize your production process!