In today’s modern world, where energy efficiency and sustainability are paramount, AC speed drives (also known as variable frequency drives, adjustable speed drives, or inverters) play a crucial role in optimizing the performance and energy consumption of electric motors. From industrial machinery to renewable energy applications, these devices are integral in controlling motor speed, reducing energy waste, and improving overall system efficiency.
What is an AC Drive and How Does It Work?
An AC drive is an electronic device used to control the speed and torque of an alternating current (AC) motor by adjusting the frequency of the power supplied to the motor. In simpler terms, it alters the motor’s speed by modifying the frequency (measured in Hertz, Hz) of the electricity provided to the motor. The basic principle is simple: the higher the frequency, the faster the motor spins; the lower the frequency, the slower the motor operates.
This ability to control motor speed with precision is vital in applications where variable speeds are required, such as in pumps, fans, conveyors, and even electric vehicles. By adjusting motor speeds, AC drives enable more efficient energy use and reduce unnecessary wear on motor components, contributing to lower maintenance costs and longer motor lifespans.
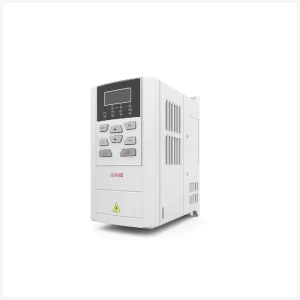
The Mechanism of Power Conversion in AC Drives
To understand how AC drives work, it’s essential to know the mechanism behind their power conversion. The power conversion circuit of an AC drive typically consists of three key components:
- Rectifier Circuit: This converts AC power into DC power.
- Intermediate Circuit: This smooths the DC voltage, stabilizing the power supply.
- Inverter Circuit: The smoothed DC is then converted back into AC power, but now with a variable frequency and voltage, suitable for controlling motor speed.
This process of converting AC to DC and back to AC involves high-speed switching of power transistors, which are semiconductor devices that control the flow of electricity. Through precise control of the switching frequency, the AC drive can generate a wide range of frequencies from the standard commercial power supply, allowing for variable-speed operation of the motor.
Power Conversion Methods: PAM vs. PWM
AC drives use different modulation techniques to control power conversion. Two common methods are Pulse Amplitude Modulation (PAM) and Pulse Width Modulation (PWM).
PAM (Pulse Amplitude Modulation) adjusts the intensity of the frequency by varying the amplitude of the pulses. This method is often used in household applications, like air conditioners, where less frequent switching is required.
PWM (Pulse Width Modulation), on the other hand, is widely used in industrial applications where precise control of speed is necessary. It converts DC voltage to three-phase AC with a prescribed switching pattern, allowing for a broad range of variable-speed operations.
While PAM is suitable for low-speed applications with less demanding load requirements, PWM provides better performance in situations that demand higher precision, such as industrial machinery or HVAC systems.
AC Drive Control Methods: V/f Control vs. Vector Control
When it comes to controlling the motor’s speed, two main control methods are commonly used: V/f control and Vector control.
V/f Control (Voltage/Frequency Control): This method maintains a constant ratio of voltage to frequency, providing basic speed control for general-purpose applications. For instance, with a 200V power supply, the AC drive would output 200V at 60Hz and 100V at 30Hz. V/f control is suitable for applications where multiple motors need to be controlled simultaneously, as the ratio of voltage to frequency is consistent.
Vector Control: Also known as field-oriented control, vector control is a more advanced method. It separates the motor current into two components: torque current, which generates the torque, and excitation current, which produces the magnetic field in the rotor. By controlling the direction of these currents through vector calculations, vector control enables precise, accurate speed control even under varying loads. This is especially useful in applications requiring high performance and reliability, such as conveyors, lifts, and precise industrial machines.
The key difference between the two is that vector control can handle load fluctuations without affecting motor speed, while V/f control may cause motor speed to vary depending on the load.
The Importance of “Slip” in Induction Motors
To understand the concept of slip, it’s essential to look at induction motors. The “slip” refers to the difference between the speed of the stator’s rotating magnetic field and the rotor’s actual speed. This slight delay is necessary for torque generation in induction motors. As the motor load increases, so does the slip, leading to a decrease in speed.
In vector control, slip is continuously calculated in real-time and compensated for, enabling constant-speed control even with varying loads. In contrast, V/f control cannot compensate for slip as effectively, meaning the motor speed may decrease if the load increases (such as when a conveyor belt carries a heavier load).
Applications of AC Drives
The applications of AC drives are diverse and span across multiple industries:
- Industrial Automation: AC drives are extensively used in manufacturing plants, processing industries, and other industrial settings to regulate motor speed in machinery like pumps, compressors, and fans.
- HVAC Systems: In heating, ventilation, and air conditioning systems, AC drives ensure that motors run efficiently, adjusting speeds to meet demand while reducing energy consumption.
- Pumps and Fans: By adjusting the speed of pumps and fans, AC drives optimize energy consumption, particularly in water treatment plants, mining, and other industries that rely on fluid handling.
- Renewable Energy: In solar, wind, and tidal energy generation, AC drives help convert energy to a usable form, enabling efficient transmission to the electrical grid.
Environmental and Energy Efficiency Benefits
AC drives not only optimize the performance of electric motors but also contribute to sustainability by significantly reducing energy consumption. In fact, it’s estimated that AC drives could reduce global electrical energy consumption by 10% if used in every suitable application. Even small adjustments to motor speed can result in large reductions in energy use, helping businesses and industries cut down on operating costs while reducing their carbon footprint.
Conclusion
AC drives are essential in modern industry, offering unparalleled control over electric motors while enhancing efficiency and reducing energy usage. Whether in manufacturing, HVAC systems, or renewable energy applications, AC drives ensure that systems run efficiently, saving energy and costs while promoting sustainability. By controlling motor speed, AC drives play a vital role in a world that demands smarter energy solutions and greater environmental responsibility.
To explore how AC drives can benefit your operations, contact us at GTAKE and discover the power of advanced motor control solutions.