Variable Frequency Drives (VFDs) are essential components in controlling the speed and torque of AC induction motors, commonly used in various industrial applications such as pumps, fans, and conveyors. VFDs regulate the motor’s speed by adjusting the frequency of the supplied voltage. There are two primary methods of control in VFDs: scalar control and vector control. Each method has its own set of advantages and limitations, making them suitable for different applications. This article will explore both methods in detail and provide insight into how they impact motor performance.
Scalar Control: V/f Control
Scalar control, also known as V/f (Voltage to Frequency) control, is the simpler of the two methods. It works by adjusting the ratio of the voltage to the frequency supplied to the motor to maintain a constant magnetic flux. The primary goal of scalar control is to ensure that the strength of the motor’s magnetic field remains constant, which results in consistent torque production.
The operation of scalar control is relatively straightforward. When the motor is at low speeds, the VFD adjusts the voltage to maintain a consistent ratio with the frequency. As the frequency increases, so does the voltage, thereby maintaining a constant ratio between the two. This method is often implemented in an open-loop configuration, where no feedback from the motor is used to correct the system’s performance. However, closed-loop implementations are possible when motor feedback is incorporated, but this adds complexity and cost to the system.
The simplicity of scalar control makes it a cost-effective option, especially for applications where precise speed regulation is not critical. It is commonly used for applications with variable loads that do not require high-performance motor control. Speed regulation is typically within a range of 2 to 3 percent of the motor’s rated speed. One of the significant benefits of scalar control is its ability to operate without the need for sophisticated feedback devices, making it a popular choice for controlling multiple motors simultaneously.
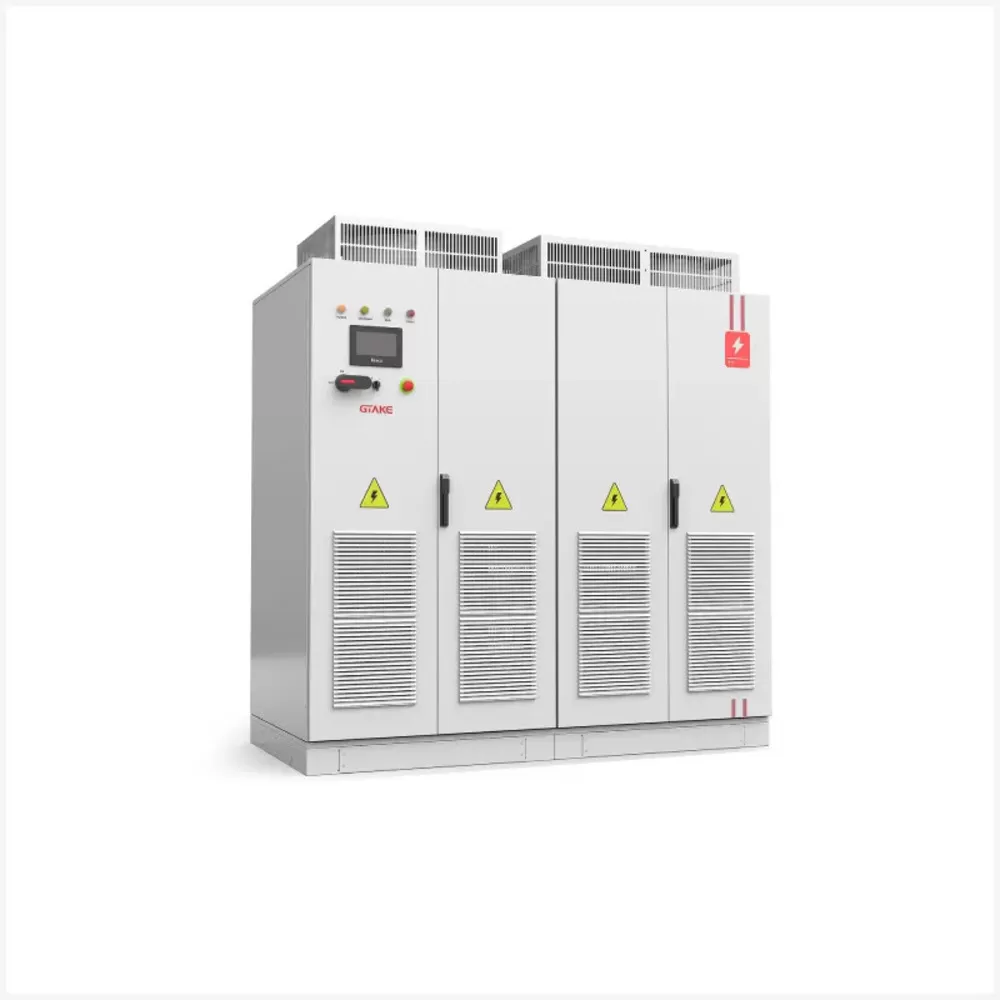
Vector Control: Field-Oriented Control (FOC)
In contrast to scalar control, vector control—often referred to as field-oriented control (FOC)—is a more sophisticated method used to control the speed and torque of AC motors with greater precision. The fundamental principle of vector control is to treat the motor’s stator current as a vector that is split into two components: the magnetizing component (d) and the torque-producing component (q). These two components are controlled independently, allowing for more accurate and dynamic control of the motor.
The d-axis current component represents the magnetizing current, while the q-axis component represents the current responsible for generating torque. By controlling these components separately, vector control maximizes the torque production and optimizes the motor’s performance across a wide range of speeds.
Unlike scalar control, which operates based on a fixed voltage-to-frequency ratio, vector control dynamically adjusts the motor’s current to ensure that the torque-producing component is kept orthogonal to the rotor flux. This results in higher efficiency, especially at low speeds or when high torque is required. Vector control can be implemented in both open-loop and closed-loop configurations.
Sensorless Vector Control
One variant of vector control is sensorless vector control, also known as sensorless FOC. In this method, instead of relying on physical feedback devices like encoders to measure the motor’s position, the system uses mathematical models of the motor’s behavior. The controller monitors the motor’s voltage and current, compares them to the expected values from the model, and adjusts the current delivered to the motor to correct any discrepancies. This approach eliminates the need for position sensors, reducing the cost and complexity of the system.
Sensorless vector control is highly effective for applications requiring precise torque and speed control at low speeds or under varying load conditions. It offers significant benefits in terms of performance, efficiency, and cost, making it an attractive option for industrial automation.
Closed-Loop Vector Control
For even more precision, closed-loop vector control incorporates position feedback devices such as encoders to provide real-time information about the motor’s position and speed. This allows for direct torque control across all operating conditions, including dynamic braking and regeneration. Closed-loop vector control can deliver up to 200% of the motor’s rated torque at zero speed, making it ideal for applications where high torque at low speeds is essential, such as in hoists or elevators.
Benefits of Vector Control Over Scalar Control
Vector control offers several advantages over scalar control, particularly in applications that demand higher precision and performance. These benefits include:
- Improved Efficiency: By independently controlling the magnetizing and torque-producing components, vector control can optimize motor performance and reduce energy losses.
- High Torque at Low Speeds: Sensorless vector control enables high torque production even at low speeds, making it suitable for applications requiring precise control, such as robotics or material handling systems.
- Better Speed and Torque Control: Closed-loop vector control provides superior speed and torque regulation, essential for dynamic operations like braking or load-holding in demanding applications.
- Reduced Stress on the Motor: Vector control systems are designed to minimize stress on the motor, reducing mechanical wear and extending the lifespan of the motor and associated equipment.
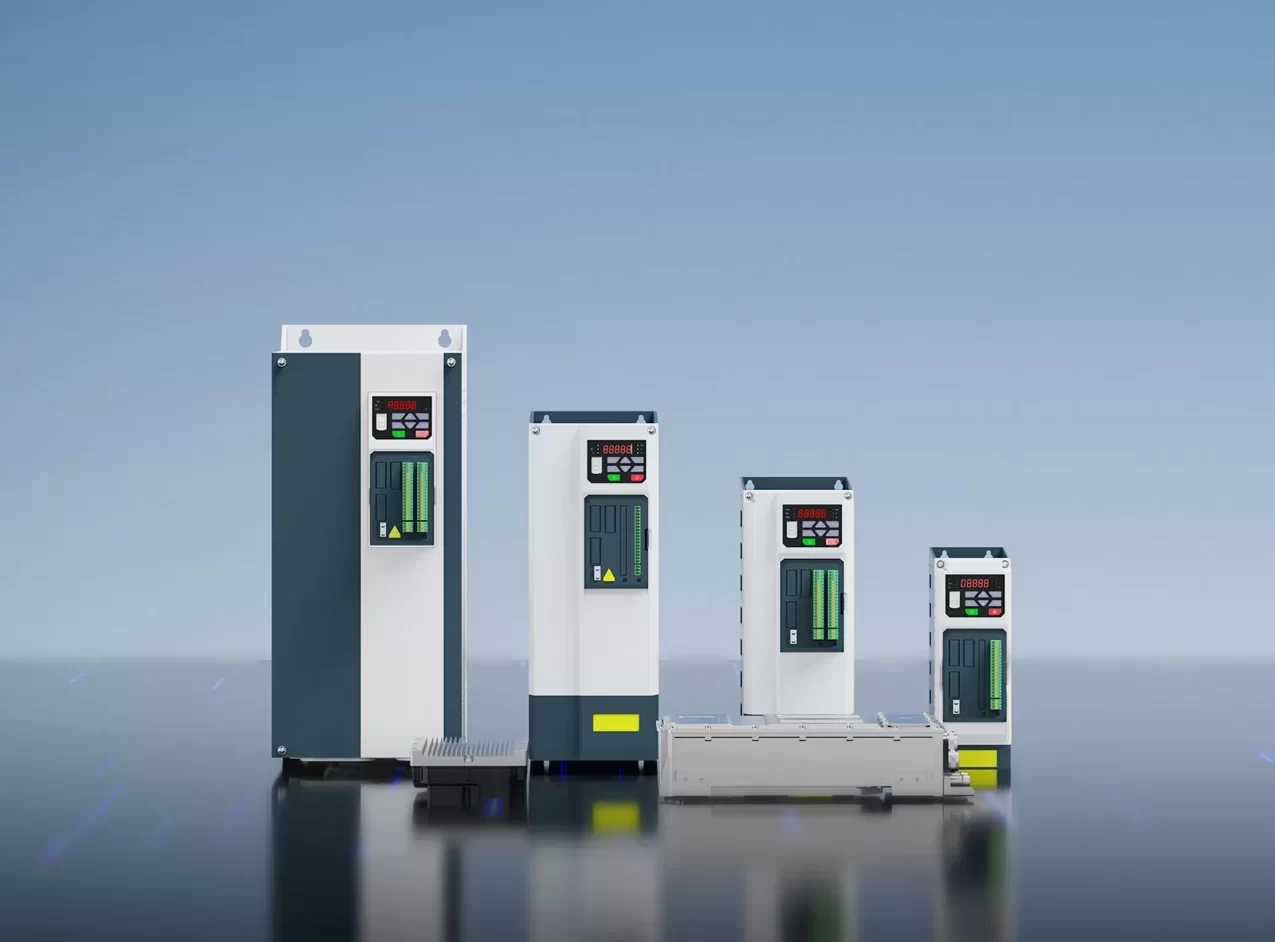
Conclusion
Choosing between scalar and vector control for VFDs depends on the specific needs of the application. Scalar control is a cost-effective solution for general-purpose applications with relatively simple speed control requirements, while vector control is ideal for high-performance applications requiring precise torque and speed regulation. As technology continues to evolve, the use of sensorless vector control is expected to grow, offering a more affordable and efficient alternative to traditional vector control methods.
By understanding the differences between these two control methods, engineers and system designers can make more informed decisions about motor control, ensuring optimal performance, energy efficiency, and reliability. With advancements in technology, particularly in microprocessor capabilities, vector control will continue to play an essential role in modern industrial applications, offering enhanced control and flexibility.
For industries looking to enhance motor control and improve energy efficiency, GTAKE offers innovative solutions in motor control, including both scalar and vector-based technologies. Our drives integrate cutting-edge technologies to provide superior performance, reliability, and energy savings for industrial and clean energy markets. Contact us to learn more about how our variable frequency drives can help optimize your systems.